【 コーティング 】
樹脂コーティングする際に、製品を吊る為に別途吊り具を使用するのですが、下画像の製品では穴形状の箇所を吊る事でコーティングをしておりました。
コーティング後、吊り具に樹脂が絡むような状態になるせいか、穴形状がスッキリせず、外観検査でバリをカッターで削ぎ落とす作業が付加してしまうことが多く、
外観を綺麗に仕上げたい、また作業性も上げたいということで、最適な吊り具を社内で内製試作しトライしてみたところ、
画像(3)(6)の通り、綺麗な穴形状に仕上げられ、バリ取り作業もかなり軽減しました。
弊社の得意とする線材加工を利用し、コーティングの仕上がりや作業性を改善出来た点が有意義な事例となりました。
画像(1)
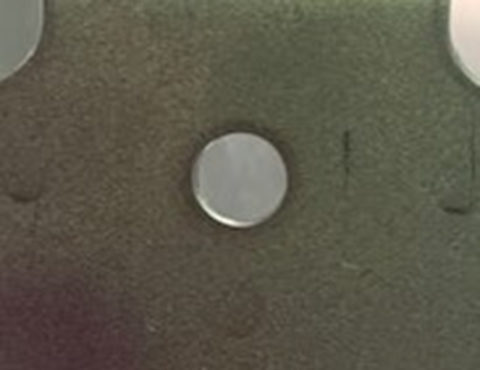
〈表面〉
(コーティング前)
画像(2)
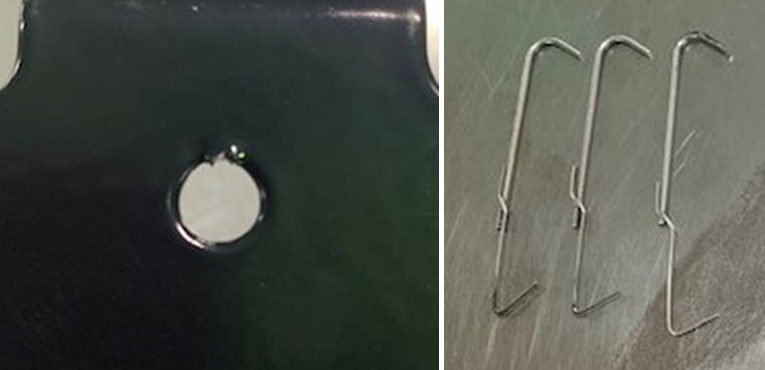
〈表面〉
(コーティング後~以前の吊り具)
*バリが目立ち、余り美しいとは言えない仕上がりです。
画像(3)
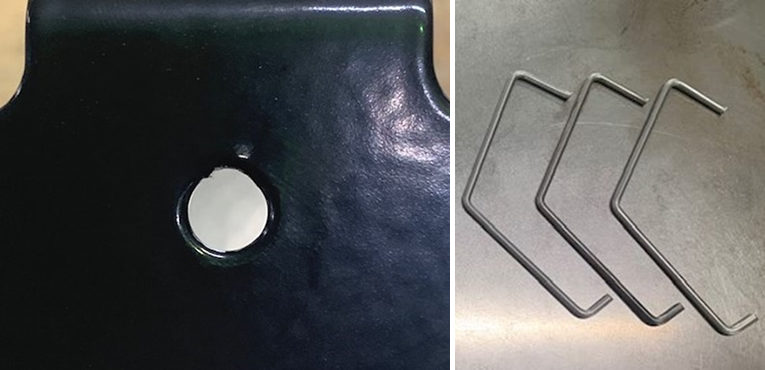
〈表面〉
(コーティング後~改善吊り具)
*スッキリとした穴形状になった事がわかると思います。
画像(4)
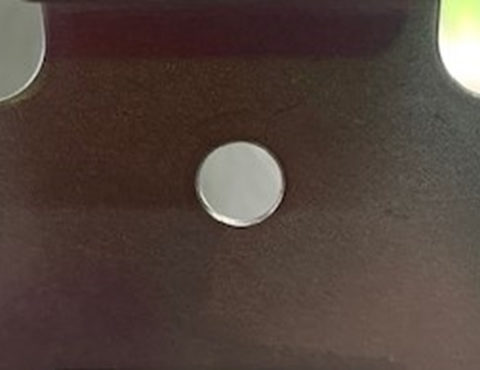
〈裏面〉
(コーティング前)
画像(5)
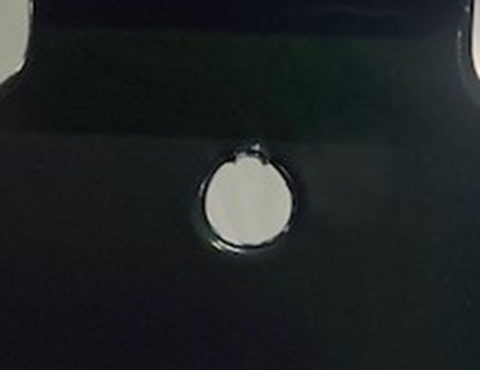
〈裏面〉
(コーティング後~以前の吊り具)
画像(6)
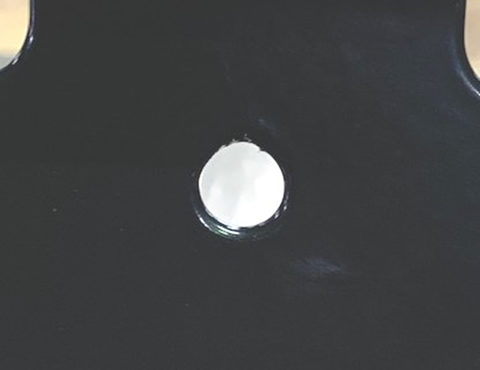
〈裏面〉
(コーティング後~改善吊り具)
【 先入れ先出し 】
実際のところ、製品の先入れ先出しをする事は非常に手間になることが多く、苦労するところです。
完成品・仕掛品を台車やスキット等を利用して所定の置き場所に移動し、時系列で製品を出荷するための積み替え作業をすることは負担が多いと言えます。
またスキットを利用すると、生産場所を狭くさせてしまう事にも繋がり、作業性の悪い環境に陥りがちです。
そこで試験的に、移動を誰でも出来る様に日毎・製品毎で木製平台車を利用してみることにしました。
その結果、完成品・仕掛品が必要以上に生産場所に止まらず、また先入れ先出しへの展開もスムーズになりました。
現在は、平台車の数を増やし、社内の必要だと思われる場所に展開しております。
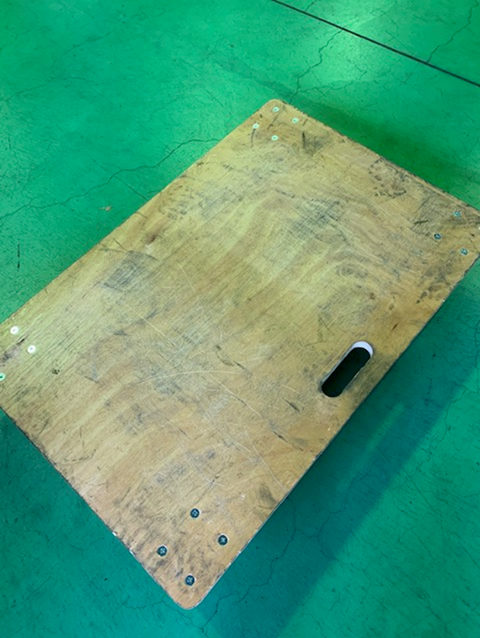
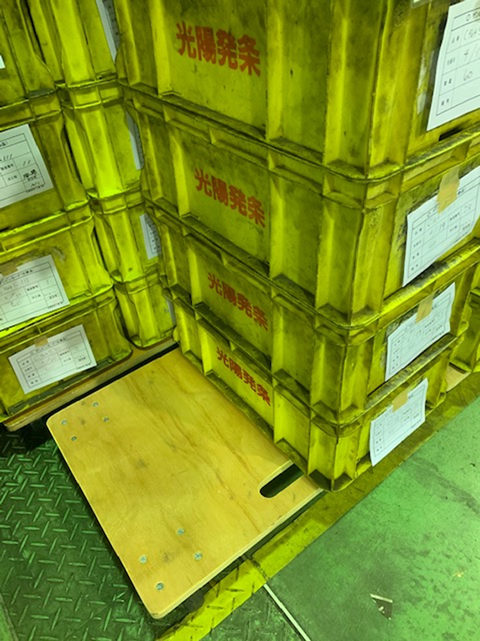